DIN 1.2379 Cold Work Mould Steel Bars with ANSI D2 Steel Grade
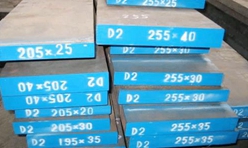
1.2379 Cold Work Mould Steel Bars with ANSI D2 Steel Grade
1 1.2379 Introduction:
1.2379 D2 steel is a high carbon – high chromium air hardening tool steel, heat treatable to 60-62 HRC. D2 offers excellent wear and abrasion resistance, due to large volumes of carbides in the micro-structure. D2 steel is widely used in long production cold work applications requiring very high wear resistance and high compression strength. It is machinable in the annealed condition, and, like other air hardening tool steels, exhibits minimal distortion in heat treat. D2 steel is available in de-carb free rounds, flats, and squares, as well as ground flat stock and drill rod.
2 1.2379 Applications:
1.2379 Typical applications are blanking, forming, and trim dies, gages, slitting cutters, wear parts, lamination dies, thread rolling dies, drawing dies, rotary cutting dies, knurls, bending dies, gages, shear blades, burnishing tools, rolls, machine parts, master parts, injection screw and tip components, seaming rolls, extrusion dies, tire shredders, scrap choppers, Stamping dies, Forming Dies, Punches, Forming Rolls, Knives, slitters, shear blades, Tools, Scrap choppers, Tyre shredders, etc.
3 1.2379 Quality Standard:
ASTM A681 – 08 Standard Specification for Tool Steels Alloy.
4 All Grades Comparison:
ASTM | Material No. | DIN | EN |
---|---|---|---|
D2 | 1.2379 | X155CrVMo12-1 | X160CrMoV121 |
5 1.2379 Chemical Composition(%)
C | Si | Mn | P | S | Cr | Mo | V |
---|---|---|---|---|---|---|---|
1.40-1.60 | 0.10-0.60 | 0.10-0.60 | 0.030 max | 0.030 max | 11.0-13.0 | 0.70-1.20 | 0.50-1.10 |
6 1.2379 HEAT TREATMENT:
- FORGING: 1.2379 Heating for forging must be done slowly and uniformly. Soak through at 1850°-1950°F and reheat as often as necessary, stopping work when the temperature drops below 1700°F. After forging, cool slowly in lime, mica, dry ashes or furnace. D2 steel should always be annealed after forging.
- ANNEALING: 1.2379 Heat slowly to 1550°-1600°F, hold until entire mass is heated through, and cool slowly in the furnace (40°F per hour) to about 1000°F, after which cooling rate may be increased. Suitable precautions must be taken to prevent excessive carburization or decarburization.
- STRESS RELIEVING: When desirable to relieve the strains of machining, heat slowly to 1050°-1250°F, allow to equalize, and then cool in still air (Strain Relieving).
- PREHEAT PRIOR TO HARDENING: Preheat slowly to 1350°-1450°F and hold at this temperature until material is uniformly heated.
- HARDENING:After thorough preheating, heat to 1800°-1850°F. Hold the work piece at the hardening temperature until it is completely and uniformly heated.
- QUENCHING: D2 1.2379 steel is an air hardening steel and will develop hardness on cooling in still air. To avoid scaling and prevent decarburization of the work piece surface, controlled atmosphere or vacuum furnaces are recommended. If these furnaces are not available, pack hardening, salt baths or wrapping the piece in stainless steel foil will provide some degree of surface protection in the hardening process. Parts should be allowed to cool to 150F, or to where they can be held in the bare hand, and then temper immediately.
- TEMPERING: The tempering temperature may be varied according to the desired hardness. If maximum hardness is desired, tempering should be in the range 300°-400°F, but if a lower hardness is acceptable, tempering at 950°F will give the optimum combination of hardness and toughness.
7 Mill′s test certificate:
EN 10204/3.1 with all relevant data reg. chem. composition, mech. properties and results of testing.