100CrMn6 1.3520 Oil Hardening Tool Steel
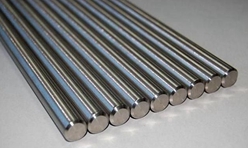
100CrMn6 1.3520 Oil Hardening Tool Steel
1. 100CrMn6 Introduction:
Medium alloy, oil hardening tool steel, which is hard-wearing.
2. 100CrMn6 Applications:
Roller bearings with thickness up to 50 mm.
3.Quality Standard:
DIN 17230-1980 Ball and Roller Bearing Steels
4.All Grades Comparison:
Material No. | EN |
---|---|
1.3520 | 100CrMn6 |
5. 100CrMn6 Chemical Composition(%)
C | Si | Mn | P | S | Cr | Ni | Cu |
---|---|---|---|---|---|---|---|
0.90-1.05 | 0.50-0.70 | 1.00-1.20 | 0.030 max | 0.025 max | 1.40-1.65 | 0.30 max | 0.30 max |
Smelting Option
1 EAF: Electric Arc Furnace
2 EAF+LF+VD: Refined-smelting and vacuum degassing
3 EAF+ESR: Electro Slag Remelting
4 EAF+PESR: protective atmosphere Electro Slag Remelting
5 VIM+PESR: Vacuum induction melting
Forming Option
1 Hot rolling process
2 Hot Forging: Electro-hydraulic; High-speed-hydraulic; Oil-hydraulic; Precision-forging
Heat-treatment Option
1 +A: Annealed (full/soft/spheroidizing)
2 +N: Normalized
3 +NT: Normalized and tempered
4 +QT: Quenched and tempered (water/oil)
Suface Option
1 Black Surface
2 Grounded: Bright but rough ; Not precision
3 Machining for plate: Bright and precision; Little turning scar
4 Peeled/Turned: Bright and precision; Little turning scar
5 Polished: Very Bright and precision size; Not turning scar
Other Services
1 Cutting: Small pieces
2 CNC Machine: Produce as your drawing
3 Package: Bare/Nylon/Canvas/Wooden
4 Payment:T/T, L/C, O/A(request credit)
5 Transport:FOB/CFR/CIF/DDU/DDP (train/ship/Air)
6.HEAT TREATMENT:
- NORMALIZING: Normalizing temperature: 860-900oC.
- SOFT ANNEALING: Heat to 760-800oC, cool slowly in furnace. This will produce a maximum Brinell hardness of 217.
- STRESS RELIEVING: Stress relieving to remove machining stresses should be carried out by heating to approx. 650oC, holding for 1-2 hours at heat, followed by air cooling. This operation is performed to reduce distortion during heat treatment.
- HARDENING: Harden from a temperature of 830-890oC followed by oil quenching. Hardness after quenching is approx. 64 HRC.
- TEMPERING: Tempering temperature: 150-180oC.
7.Mill′s test certificate:
EN 10204/3.1 with all relevant data reg. chem. composition, mech. properties and results of testing.