1.2312 P20+S Plastic Mold Steel
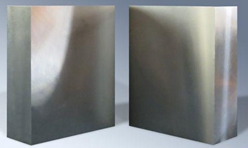
1.2312 P20+S Plastic Mold Steel
1 1.2312 Introduction
P20+S Plastic mold steel with excellent machinability properties because of the high S content, good toughness properties, good wear resistance, uniform hardness in all dimensions, dimensional stability, requiring no heat treatment, 280-325HB hardened and tempered condition, suitable for nitriding to increase wear resistance, not suitable for chrome plating, polishing and etch graining.
2 1.2312 Applications
P20+S Plastic Mold Steel is ideally suited for the production of moulds where improved machinability is required. Typical applications include die holders, zinc die casting dies, backers, bolsters and injection moulds. The versatility of this plastic mould tool steel with its high tensile characteristics enables uses for a variety of other applications such as shafts and wear strips.
3 Quality Standard
:
ASTM A681 Standard Specification for Tool Steel
4 All Grades Comparison
ASTM A681 | Werkstoff |
---|---|
P20+S | 1.2312 |
5 Chemical Composition(%)
C | Si | Mn | P | S | Cr | Mo |
---|---|---|---|---|---|---|
0.35-0.45 | 0.30-0.50 | 1.40-1.60 | 0.030 max | 0.05-0.10 | 1.80-2.00 | 0.15-0.25 |
6 HEAT TREATMENT
Forging: Heat slowly, allowing sufficient time for the steel to become heated through. Begin forging at 1050°C. Do not forge below 930°C reheating if necessary. After forging, cool very slowly.
Annealing: Heat uniformly to 710-740°C. Soak well, cool slowly in the furnace.
Stress Relieving:When dies are heavily machined, we recommend stabilising just before finish machining in order to relieve machining strains. Heat to 460-500°C. Soak well and allow to cool in the air.
Hardening: Heat uniformly to 830-870°C until heated through. Quench in oil.
Tempering: Heat uniformly and soak at the tempering temperature for at least one hour per 25mm of section. Allow to cool in still air.
Tempering Temperature | Hardness(HRC) | Tensile Strength (Mpa) |
---|---|---|
100oC | 51 | 1730 |
200oC | 50 | 1670 |
300oC | 48 | 1570 |
400oC | 46 | 1480 |
500oC | 42 | 1330 |
600oC | 36 | 1140 |
7 Nitriding:
Tools machined from pre-hardened P20+S Plastic Mold Steel may be nitrided to give a wear resistant case of approximately Rockwell C60 surface hardness with a case depth of 0.35mm to 0.5mm. Nitriding also increases the corrosion resistance. After nitriding at 525°C in ammonia gas the surface hardness of the tool will be approximately 650HV.
Temperature | Time (hours) | Approx. Depth of Case (mm) |
---|---|---|
525oC | 20 | 0.3 |
525oC | 40 | 0.35 |
525oC | 60 | 0.50 |
Case Hardening: Tools produced from P20+S Plastic Mold Steel may be case hardened, which can achieve a surface hardness of between 55 to 59 Rockwell C.
Hard Chromium Plating: To avoid hydrogen embrittlement P20+S Plastic Mold Steel should be tempered for 4 hours at 180°C for 4 hours after hard chromium plating
Induction Hardening:Induction or flame hardening of will achieve a hardness of 50 to 55HRc. It is preferable to air cool, though smaller components may require forced cooling. Temper immediately after hardening.
8 1.2312 Mill′s test certificate
EN 10204/3.1 with all relevant data reg. chem. composition, mech. properties and results of testing.