20MnCr5 1.7147 SAE 5120 Case Hardening Steel
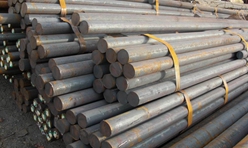
20MnCr5 DIN1.7147 SAE5120 Case Hardening Steel
1 20MnCr5 Applications
it is a case-hardening steel with low carbon content but good hardenability reaching good wear resistance due to high surface hardness after hardening. The small grain size benefits in good ductility and fatigue strength.
Alloyed case hardening steel for parts with a required core tensile strength of 1000 – 1300 N/mm² and good wearing resistance as boxes, piston bolts, spindles, camshafts, gears, shafts and other mechanical controlling parts.
2 All Grades Comparison:
DIN | Material No. | AFNOR | SAE | UNI |
---|---|---|---|---|
20MnCr5 | 1.7147 | 20MC | 5120 | 20MnCr5 |
3 20MnCr5 Quality Standard:
BS EN 10084 2008 Case hardening steels
4 20MnCr5 Chemical Composition(%)
C | Mn | Si | P | S | Cr |
---|---|---|---|---|---|
0.17–0.22 | 1.10–1.40 | 0.40 max | 0.035 max | 0.035 max | 1.00–1.30 |
5 Mechanical Properties( T=20°C if not differently stated )
Heat treatment state | Diameter(mm) | Rm (Mpa) |
---|---|---|
QUENCHED AND TEMPERED | 16 max | 1200 min |
QUENCHED AND TEMPERED | 16-40 | 1000 min |
QUENCHED AND TEMPERED | 40-100 | 800 min |
6 HEAT TREATMENT AND HOT PLASTIC DEFORMATION TEMPERATURES
Process | TEMPERATURE ° C | Cooling Medium |
---|---|---|
Forging or hot rolling | 850-1100 | air |
Normalizing | 840-870 | air |
Soft Annealing | 650-700 | furnace 217HB max |
Carburising | 880-980 | / |
Core hardening | 860-900 | oil |
Intermediate annealing | 650-700 | / |
Case hardening | 780-820 | oil |
Tempering | 150-200 | / |