17CrNi6-6 DIN 1.5918 Engineering Steels
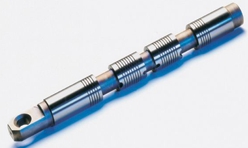
17CrNi6-6 1.5918 Engineering Steels
1. 1.5918 Introduction
Structural, pressure vessel and engineering steels. 1.5918 is the EN numeric designation for this material. 17CrNi6-6 is the EN chemical designation. It has a moderately high density among EN wrought alloy steels. In addition, it has a moderately high electrical conductivity and a moderately high base cost.
2. 1.5918 Application
Alloyed case hardening steel for highly strained parts and good toughness at core tensile strength of 900 – 1200 N/mm². Driving bevel gears, crown wheels, gears, shafts, bolts for automotive and gear components. Steel used mainly in the engineering industry for medium sized, heavily loaded components requiring high surface hardness. The chemical composition is similar to the 17HNM, 18CrNiMo7-6, 1.6587 grades. It is distinguished by a slightly lower carbon content and the absence of Molybdenum. Products made of 15HN steel and its substitutes are used in the production of gears, pivots, transmissions or shafts of machines, cars and engines requiring high ductility, abrasion resistance, variable loads and impact resistance during continuous operation.
3.All Grades Comparison
DIN | EN |
---|---|
1.5918 | 17CrNi6-6 |
4.Quality Standard
EN 10084: 2008 Case hardening steels. Technical delivery conditions
EN 10263-3: 2001 Steel rod, bars and wire for cold heading and cold extrusion. Technical delivery conditions for case hardening steels
5. 1.5918 Chemical Composition(%)
C | Mn | Si | P | S | Cr | Ni |
---|---|---|---|---|---|---|
0.14-0.20 | 0.50-0.80 | 0.40 max | 0.025 max | 0.035 max | 1.40-1.70 | 1.40-1.70 |
6.Mechanical Properties(T=20°C if not differently stated)
Process | Diameter(mm) | Tensile Strength Rm (Mpa) | Hardness (HB) |
---|---|---|---|
Treated to improve shearability | / | / | 255 max |
SOFT ANNEALED | / | / | 229 max |
Treated for strength | / | / | 175-229 |
Treated for ferrite and pearlite structure and hardness range | / | / | 156-207 |
QUENCHED AND TEMPERED | 16 max | 1200 min | / |
QUENCHED AND TEMPERED | 16-40 | 1100 min | / |
QUENCHED AND TEMPERED | 40-100 | 900 min | / |
7.HEAT TREATMENT:
Process | Temperature(oC) | Media |
---|---|---|
Forging or hot rolling | 1100-850 | / |
Normalising | 850-880 | air |
Soft annealing | 650-700 | furnace |
Carburising | 880-980 | / |
Core hardening | 830-870 | oil |
Intermediate annealing | 630-650 | / |
Case hardening | 780-820 | oil |
Tempering | 150-200 | / |
8.Mill′s test certificate:
EN 10204/3.1 with all relevant data reg. chem. composition, mech. properties and results of testing.
Delivery Condition
1.Shape:Round/Square / Flat/Shafts/Rollers/Blocks
2.Surface condition:Black surface/Bright surface
3.Heat Treatment:Normalized/Annealed/QT
4.Straightness:Max 3mm/m(Enhanced straightness may be available on request)
5.Length:3000-5800mm suitable for 20″container. above 6000mm,suitable for 40″ container
6.Grain Size: 5-8 acc to ASTM E112-96
7.Ultrasonic Standard: Sep1921/ASTM A388/EN 10228-3
8.Non Metallic Inclusion: 2 max acc to ASTM E45 /K4≤20 acc to DIN 50602
9.Forging Ratio: minimum 4 : 1
10.Marking: Grade/Weight/Length/Size/Heat Number
Quality Certification
A material test report(Inspection Certificate EN 10204 3.1) will be provided, documenting the following:
1.Chemical analysis
2.Mechanical properties
3.Surface hardness
4.Non Metallic Inclusion
5.Heat Treatment Process
6.Grain size
7.Forging ratio
8.NDE test method/criteria
Other designations of the grade:
15HNA, 15CrNi6, 1.5919, 15 CrNi 6, 14NiCr6, 17CrNi16, 17 CrNi 16, BNC5, 15Cr6Ni6, UNS H43200, UNS H43204, AISI 4320H, AISI 4320, AISI 3115, C5420, 17Х2ГН2, 17H2GN2, 16NiCr6, ZF1, 17CrNi6-6, 1.6757, 1.5918.