SAE 9254 Spring Steel
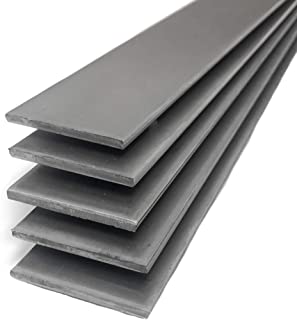
SAE-AISI 9254 (G92540) Silicon-Chromium Steel
SAE-AISI 9254 steel is an alloy steel formulated for primary forming into wrought products. Cited properties are appropriate for the annealed condition. 9254 is the designation in both the SAE and AISI systems for this material. G92540 is the UNS number. AISI 9254 is a Standard grade Alloy Steel. It is commonly called AISI 9254 Silicon-manganese steel. It is composed of (in weight percentage) 0.51-0.59% Carbon (C), 0.60-0.80% Manganese (Mn), 0.035%(max) Phosphorus (P), 0.04%(max) Sulfur (S), 1.20-1.60% Silicon (Si), 0.60-0.80% Chromium (Cr), and the base metal Iron (Fe). Other designations of AISI 9254 alloy steel include UNS G92540 and AISI 9254.
AISI-9254 Chemical component
C(%) | Si(%) | Mn(%) | P(%) | S(%) | Cr(%) |
0.51-0.59 | 1.2-1.6 | 0.6-0.8 | ≦0.035 | ≦0.04 | 0.6-0.8 |
Relate Steel Type
Steel Type | Country Code | C(%) | Si(%) | Mn(%) | P(%) | S(%) | Cr(%) | Yield stress (Mpa) |
SUP12 | CNS | 0.51-0.59 | 1.2-1.6 | 0.6-0.9 | ≦0.035 | ≦0.035 | 0.6-0.9 | ≧1080 |
SUP12 | JIS | 0.51-0.59 | 1.2-1.6 | 0.6-0.9 | ≦0.035 | ≦0.035 | 0.6-0.9 | ≧1080 |
9254 | AISI | 0.51-0.59 | 1.2-1.6 | 0.6-0.8 | ≦0.035 | ≦0.04 | 0.6-0.8 |
The fatigue resistance is a property that exerts a strong influence on the suspension spring performance in vehicles. The choice of SAE 9254 steel was due to its wide use in the manufacture of these springs and their fatigue properties and toughness. The manufacture of SAE 9254 steel springs has been made by the hot winding process and the heat treatment by conventional quenching and tempering or by cold winding process and induction hardening and tempering. The shot peening induced a compressive residual stress which increased the fatigue life of the SAE 9254 steel. The residual stress profile from the surface of springs showed a peak in the values of the compressive stress for both manufacturing processes. The maximum residual stress in the cold processed spring was higher than the hot processed spring and maintained much higher values along the thickness of the spring from the surface, resulting from manufacturing processes. The fatigue cracking of the springs, without shot peening, started by torsional fatigue process, with typical macroscopic propagation. The fracture surface showed stretch marks with high plastic deformation.
Mechanical Properties
Properties | Conditions | ||
T (°C) | Treatment | ||
Density (×1000 kg/m3) | 7.7-8.03 | 25 | |
Poisson’s Ratio | 0.27-0.30 | 25 | |
Elastic Modulus (GPa) | 190-210 | 25 | |
Tensile Strength (Mpa) | 1158 | 25 | oil quenched, fine grained, tempered at 425°C |
Yield Strength (Mpa) | 1034 | ||
Elongation (%) | 15 | ||
Reduction in Area (%) | 53 | ||
Hardness (HB) | 335 | 25 | oil quenched, fine grained, tempered at 425°C |
Thermal Properties
Properties | Conditions | ||
T (°C) | Treatment | ||
Thermal Conductivity (W/m-K) | 42.7 | 100 | |
Specific Heat (J/kg-K) | 477 | 50-100 |
Physical Properties
Quantity | Value | Unit |
Thermal expansion | 16 – 17 | e-6/K |
Thermal conductivity | 16 – 16 | W/m.K |
Specific heat | 500 – 500 | J/kg.K |
Melting temperature | 1370 – 1400 | °C |
Service temperature | 0 – 500 | °C |
Density | 8000 – 8000 | kg/m3 |
Resistivity | 0.7 – 0.7 | Ohm.mm2/m |