ASTM A228 Music Wire
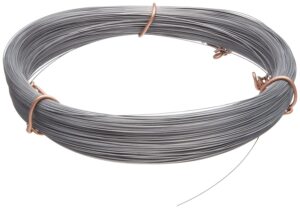
ASTM A228 Music Wire
Music wire, also known as piano wire or spring wire, is a high-carbon steel alloy famous for its high tensile strength and high elastic limit. Music wire derived its name from one of its most popular applications, piano strings. However, this versatile steel alloy has many different high-stress applications. The components that make this material type include Carbon (C) and Manganese (Mn). The maximum temperature it is able to resist is of 250º Fahrenheit (121º Celsius) and it is not corrosive resistant so if you wish to use this material type in a moist or corrosive environment, you might want to have the springs go under plating.
Music wire has high tensile strength, high ductility and excellent fatigue life. Our music wire meets the latest revisions of ASTM A228/A228M-16.Type I : wire shall be directly drawn from either as-rolled rods or from air patented rods or wire to the final wire diameter.Type II : wire shall be drawn from either patented rod or patented wire to the final wire diameter. All patenting is not allowed.
ASTM A228/A228M-18 Standard Specification For Steel Wire, Music Spring Quality This specification covers high quality, round, cold-drawn steel music spring quality wire for the manufacture of springs subject to high stresses or requiring good fatigue properties. The steel shall either be ingot cast or strand cast. Heat and product analysis shall be performed wherein steel materials shall conform to required chemical compositions of carbon, manganese, phosphorus, sulfur, and silicon. Steel specimens shall also undergo tension test, wrap test, and torsion tests This specification covers two types of round, cold-drawn steel music spring quality wire, uniform in mechanical properties, intended especially for the manufacture of springs subject to high stresses or requiring good fatigue properties.
ASTM A228 music wire is a carbon (non-alloy) steel formulated for primary forming into wrought products. Cited properties are appropriate for the cold worked (strain hardened) condition. ASTM A228 is the defining standard for this material. K08500 is the UNS number. It has the highest tensile strength among wrought carbon or non-alloy steels. In addition, it has a fairly low ductility and a moderately low thermal conductivity.
Music Wire Spring Properties Definition
Wire spring which is manufactured using Music Wire; the American Standard of Trade and Measure (ASTM) for this material type is A228. It is a high carbon spring steel and it is the most commonly used. It offers uniform tensile strength which, when coupled with a good wire spring design, will offer many thousands of cycles of spring life. Used to manufactured several types of wire spring types.
Table of Music Wire Properties
Nominal Analysis | C – .70 – 1.00% Mn. – .20 -60% |
Minimum Tensile Strength | 230*10^3 – 399*10^3 |
Modulus of Elasticity | 30*10^6 |
Design Stress % Minimum Tensile | 45% |
Modulus in Torsion | 11.5 |
Maximum Temperature | 250º F (121º C) |
Rockwell Hardness | C41-60 |
Method of Manufacture Chief Uses Special Properties | Cold drawn. High and uniform tensile. High quality springs and wire forms. |
Music Wire Spring
A spring made of music wire can resist the maximum temperature of 250ºF (121ºC). minimum tensile strength between 230*10^3 and 399*10^3 psi, its modulus of elasticity is 30*10^6 psi, and a rockwell hardness of C41-60. This specific material type will NOT resist a corrosive environment for it shall not be exposed to a moist/humid atmosphere.
Music Wire ASTM A228 is the most common and economical material type. This material type is also very basic which is why it runs the risk of rusting in corrosive environments or burning under very high temperatures. This is why we have provided you with the Music Wire Spring Properties chart, so that you may see if music wire will work for you or if you must go with a more exotic material type.
Our spring calculator includes Music Wire ASTM A228 as one of the material types you may use to generate a spring design. Whether it is a music wire compression spring, music wire extension spring, or music wire torsion spring; the above values shown on the table are part of the spring calculation software so that all of the values, like spring rate and maximum safe travel, are highly accurate. This way, you’re able to generate a music wire spring design and know which are its capacities and its limitations.
The spring calculator is also programmed to provide you with an instant quote if you use either Music Wire ASTM A228 or Stainless Steel 302 A313. As you enter your spring dimensions, pick either one of these material types, and click on “Calculate”, the calculator automatically takes all of the music wire spring properties and generates a live spring quote so that, not only do you get to work on your design, but you also get to buy it once you’re done. This isn’t it, though. Spring Creator will additionally provide you with stock spring suggestions in case you’re interested in buying small quantities of springs.
Last, but not least, generate a live blueprint of your music wire spring design. It is a live drawing made in proportion to the inputs you entered. You may email it to yourself or request a quote in case your parameters were out of the instant quoting range and the spring calculator didn’t automatically provide you with one. The file you will receive in your email will be in PDF format. It will include the music wire spring’s full analysis as well as the instant quote and the stock spring suggestions.
Use high carbon steel alloy music wire for applications that demand high strength and durability, such as springs, jewelry and piano and guitar strings. Music wire can withstand high tension and rugged use and still last a long time. Also find spring steel in smaller thicknesses to help fabricate lockpicks, spring clamps, antennas, and small aircraft landing gear. today for high-quality music wire in a variety of thicknesses and tensile strengths.
Music Wire ASTM A 228 |
|||||||||
Nominal Chemistry |
|
||||||||
Minimum Tensile Strength psi x 103 |
230-399 | ||||||||
E – Modulus of Elasticity psi x 106 |
30 | ||||||||
Design Stress % Minimum Tensile | 45 | ||||||||
G – Modulus in Torsion psi x 106 |
11.5 | ||||||||
Maximum Operating Temperature °F |
250 | ||||||||
Rockwell Hardness | C41-60 | ||||||||
Density lb/in3 |
0.284 | ||||||||
Shear Modulus c GPa |
11600 80.0 | ||||||||
Method of Manufacture Chief Uses Special Properties |
Music Wire is cold drawn, and it has a high and uniform tensile. Music Wire is the toughest and most widely used of all spring materials for small springs. It has the highest tensile strength and can withstand higher stresses under repeated loading than any other spring material. | ||||||||
Equivalent or Common Trade Names | 228 Music Wire Piano wire ASTM A228 ASTM A29 ASTM A682 AISI 1086 AMS 5112 QQ-W-470 UNS K08500 UNS G10860 SAE J403 SAE J412 SAE J414e Japanese JIS G3522 SWP-A G3522 SWP-B German DIN 1.1269 British BS 1408 5216 5201 |
Benefits of Music Wire Compression Springs
Music wire is a frequently used material for compression springs because it can bear repeated heavy loads while maintaining its shape and elasticity. There are many benefits associated with music wire, including:
High tensile strength
High elasticity
Affordability
Availability
Easily worked
Limitations of Music Wire Compression Springs
Although there are many benefits of choosing music wire compression springs, this material does have its disadvantages. Music wire compression springs should not be used in extreme temperatures, and they can give way under shock loads. Our team of specialists can help you decide if music wire compression springs are the right choice for your application.
Types of Music Wire Material
ASTM-A228 or AMS-5112
DIN-17223 or EN-10270-1 or JIS-3522 SWP-A/B or AMS-5112
Tensile Requirement (ASTM A228)
Dia. | T/S (ksi) | Dia. | T/S (ksi) | |||
(Inch) | MIN | MAX | (Inch) | MIN | MAX | |
0.008 | 399 | 441 | 0.067 | 290 | 321 | |
0.009 | 393 | 434 | 0.072 | 287 | 317 | |
0.010 | 387 | 428 | 0.076 | 284 | 314 | |
0.011 | 382 | 422 | 0.079 | 283 | 313 | |
0.012 | 377 | 417 | 0.080 | 282 | 312 | |
0.013 | 373 | 412 | 0.085 | 279 | 308 | |
0.014 | 369 | 408 | 0.090 | 276 | 305 | |
0.015 | 365 | 404 | 0.095 | 274 | 303 | |
0.016 | 362 | 400 | 0.100 | 271 | 300 | |
0.018 | 356 | 393 | 0.102 | 270 | 299 | |
0.020 | 350 | 387 | 0.107 | 268 | 296 | |
0.022 | 345 | 382 | 0.110 | 267 | 295 | |
0.024 | 341 | 377 | 0.112 | 266 | 294 | |
0.026 | 337 | 373 | 0.121 | 263 | 290 | |
0.028 | 333 | 368 | 0.125 | 261 | 288 | |
0.030 | 330 | 365 | 0.130 | 259 | 286 | |
0.032 | 327 | 361 | 0.135 | 258 | 285 | |
0.034 | 324 | 358 | 0.138 | 256 | 283 | |
0.036 | 321 | 355 | 0.140 | 256 | 283 | |
0.038 | 318 | 352 | 0.145 | 254 | 281 | |
0.040 | 315 | 349 | 0.150 | 253 | 279 | |
0.042 | 313 | 346 | 0.156 | 251 | 277 | |
0.045 | 309 | 342 | 0.162 | 249 | 275 | |
0.048 | 306 | 339 | 0.177 | 245 | 270 | |
0.051 | 303 | 335 | 0.192 | 241 | 267 | |
0.052 | 302 | 333 | 0.207 | 238 | 264 | |
0.055 | 300 | 331 | 0.225 | 235 | 260 | |
0.059 | 296 | 327 | 0.250 | 230 | 255 | |
0.063 | 293 | 324 |
PHOSPHATE COATED MUSIC WIRE
Dia (Inch) | Cast I.D. | Max Weight (Lbs) | Dia (Inch) | Cast I.D. | Max Weight (Lbs) | |
0.008 – 0.011 | 6″ | 11 | 0.032 – 0.054 | 16″ | 880 | |
0.012 – 0.019 | 8″ | 22 | 0.055 – 0.070 | 20″ | 1,300 | |
0.020 – 0.031 | 12″ | 110 | 0.071 – 0.117 | 24″ | 1,800 | |
0.032 – 0.054 | 16″ | 220 | 0.118 – 0.250 | 30″ | 2,200 | |
0.055 – 0.070 | 20″ | 440 | ||||
0.071 – 0.117 | 24″ | 550 | ||||
0.118 – 0.250 | 30″ | 660 |
GALVANIZED MUSIC WIRE
Dia (Inch) | Cast I.D. | Max Weight (Lbs) | Dia (Inch) | Cast I.D. | Max Weight (Lbs) | |
0.008 – 0.011 | 6″ | 11 | 0.032 – 0.054 | 16″ | 880 | |
0.012 – 0.019 | 8″ | 22 | 0.055 – 0.070 | 20″ | 1,300 | |
0.020 – 0.031 | 12″ | 110 | 0.071 – 0.079 | 24″ | 1,800 | |
0.032 – 0.054 | 16″ | 220 | ||||
0.055 – 0.070 | 20″ | 440 | ||||
0.071 – 0.079 | 24″ | 550 |
Stock extension springs are made in different material types so these wire springs may be used in different environments but the most commonly used wire type is Music Wire ASTM A228. That is why you’re able to find a great number of stock music wire extension springs at The Spring Store! Where we provide you with our extensive extension spring catalog as well as a few tools to make designing and finding the ideal stock music wire extension spring much easier.
Phosphate Coated Music Wire
DIAMETER (INCH) | TENSILE STRENGTH KSI MIN | TENSILE STRENGTH KSI MAX |
0.004 | 439 | 485 |
0.005 | 426 | 471 |
0.006 | 415 | 459 |
0.007 | 407 | 449 |
0.008 | 399 | 441 |
0.009 | 393 | 434 |
0.010 | 387 | 428 |
0.011 | 382 | 422 |
0.012 | 377 | 417 |
0.013 | 373 | 412 |
0.014 | 369 | 408 |
0.015 | 365 | 404 |
0.016 | 362 | 400 |
0.018 | 356 | 393 |
0.020 | 350 | 387 |
0.022 | 345 | 382 |
0.024 | 341 | 377 |
0.026 | 337 | 373 |
0.028 | 333 | 368 |
0.030 | 330 | 365 |
0.032 | 327 | 361 |
0.034 | 324 | 358 |
0.036 | 321 | 355 |
0.038 | 318 | 352 |
0.040 | 315 | 349 |
0.042 | 313 | 346 |
0.045 | 309 | 342 |
0.048 | 306 | 339 |
0.051 | 303 | 335 |
0.055 | 300 | 331 |
0.059 | 296 | 327 |
0.063 | 293 | 324 |
0.067 | 290 | 321 |
0.072 | 287 | 317 |
0.076 | 284 | 314 |
0.080 | 282 | 312 |
0.085 | 279 | 308 |
0.090 | 276 | 305 |
0.095 | 274 | 303 |
0.100 | 271 | 300 |
0.102 | 270 | 299 |
0.107 | 268 | 296 |
0.110 | 267 | 295 |
0.112 | 266 | 294 |
0.121 | 263 | 290 |
0.125 | 261 | 288 |
0.130 | 259 | 286 |
0.135 | 258 | 285 |
0.140 | 256 | 283 |
0.145 | 254 | 281 |
0.150 | 253 | 279 |
0.156 | 251 | 277 |
0.162 | 249 | 275 |
0.177 | 245 | 270 |
0.192 | 241 | 267 |
0.207 | 238 | 264 |
0.225 | 235 | 260 |
0.250 | 230 | 255 |
TENSILE STRENGTH CHART
Diameter, in | Tensile Strength,
ksi |
Diameter, in | Tensile Strength,
ksi |
Diameter, in | Tensile Strength,
ksi |
Diameter, in | Tensile Strength,
ksi |
||||
min | max | min | max | min | max | min | max | ||||
.004 | 439 | 485 | .022 | 345 | 382 | .059 | 296 | 327 | .125 | 261 | 288 |
.005 | 426 | 471 | .024 | 341 | 377 | .063 | 293 | 324 | .130 | 259 | 286 |
.006 | 415 | 459 | .026 | 337 | 373 | .067 | 290 | 321 | .135 | 258 | 285 |
.007 | 407 | 449 | .028 | 333 | 368 | .072 | 287 | 317 | .140 | 256 | 283 |
.008 | 399 | 441 | .030 | 330 | 365 | .076 | 284 | 314 | .145 | 254 | 281 |
.009 | 393 | 434 | .032 | 327 | 361 | .080 | 282 | 312 | .150 | 253 | 279 |
.010 | 387 | 428 | .034 | 324 | 358 | .085 | 279 | 308 | .156 | 251 | 277 |
.011 | 382 | 422 | .036 | 321 | 355 | .090 | 276 | 305 | .162 | 249 | 275 |
.012 | 377 | 417 | .038 | 318 | 352 | .095 | 274 | 303 | .177 | 245 | 270 |
.013 | 373 | 412 | .040 | 315 | 349 | .100 | 271 | 300 | .192 | 241 | 267 |
.014 | 369 | 408 | .042 | 313 | 346 | .102 | 270 | 299 | .207 | 238 | 264 |
.015 | 365 | 404 | .045 | 309 | 342 | .107 | 268 | 296 | .225 | 235 | 260 |
.016 | 362 | 400 | .048 | 306 | 339 | .110 | 267 | 295 | .250 | 230 | 255 |
.018 | 356 | 393 | .051 | 303 | 335 | .112 | 266 | 294 | |||
.020 | 350 | 387 | .055 | 300 | 331 | .121 | 263 | 290 |
Tensile strength values for intermediate diameters may be interpolated.