S2 Tool Steel
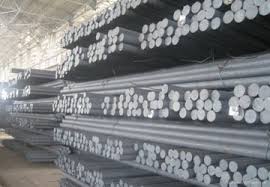
S2 Tool Steel – Shock-Resisting Steel (UNS T41902)
Introduction
Tool Steels S2 is stocked by 0 North American distributors and produced by 1 large mills. Distributors will offer small quantity buys while mills will generally only sell large quantities, with delivery times anywhere from 10 to 50 weeks depending on size and form required Shock-resisting tool steels are designated as group S steels according to the AISI classification system. These steels include S1, S2, S5, S6, and S7 types. The hardenability of group S steels can be controlled by varying thier composition rather than adjusting the melting methods and grain size. They can obtain optimum hardness at higher austenitizing temperatures. The tempering resistance of group S steels can be enhanced by the addition of silicon, which also forms a microstructure to resist distortion in tempered conditions. The following section will give an overview of S2 shock-resisting tool steels.
Chemical Composition
The following table shows the chemical composition of S2 tool steels.
Element | Content (%) |
Iron, Fe | 97.0 |
Silicon | 1.05 |
Carbon, C | 0.4-0.55 |
Molybdenum, Mo | 0.4 |
Manganese, Mn | 0.4 |
Vanadium, V | ≤0.5 |
Phosphorus, P | ≤0.03 |
Sulfur, S | ≤0.03 |
Smelting Option
1 EAF: Electric Arc Furnace
2 EAF+LF+VD: Refined-smelting and vacuum degassing
3 EAF+ESR: Electro Slag Remelting
4 EAF+PESR: protective atmosphere Electro Slag Remelting
5 VIM+PESR: Vacuum induction melting
Forming Option
1 Hot rolling process
2 Hot Forging: Electro-hydraulic; High-speed-hydraulic; Oil-hydraulic; Precision-forging
Heat-treatment Option
1 +A: Annealed (full/soft/spheroidizing)
2 +N: Normalized
3 +NT: Normalized and tempered
4 +QT: Quenched and tempered (water/oil)
Suface Option
1 Black Surface
2 Grounded: Bright but rough ; Not precision
3 Machining for plate: Bright and precision; Little turning scar
4 Peeled/Turned: Bright and precision; Little turning scar
5 Polished: Very Bright and precision size; Not turning scar
Other Services
1 Cutting: Small pieces
2 CNC Machine: Produce as your drawing
3 Package: Bare/Nylon/Canvas/Wooden
4 Payment:T/T, L/C, O/A(request credit)
5 Transport:FOB/CFR/CIF/DDU/DDP (train/ship/Air)
Physical Properties
The physical properties of S2 tool steels are given in the following table.
Properties | Metric | Imperial |
Density | 7.79 g/cc | 0.281 lb/in3 |
Melting point | 1421°C | 2590°F |
Mechanical Properties
The mechanical properties of S2 tool steels are tabulated below.
Properties | Conditions | ||
T (°C) | Treatment | ||
Poisson’s ratio | 0.27-0.30 | 25 | – |
Elastic modulus | 190-210 GPa | 25 | – |
Thermal Properties
The following table shows the thermal properties of S2 tool steels.
Properties | Conditions | ||
T (°C) | Treatment | ||
Thermal expansion | 10.9 x 10-6/ºC | 20-100 | – |
Other Designations
Other designations that are equivalent to S2 tool steels include:
ASTM A681
FED QQ-T-570
SAE J437
SAE J438
UNS T41902
Fabrication and Heat Treatment
Machinability
The machinability rating of S2 tool steels is 85% of that of the W group steels.
Forming
S2 tool steels are formed using conventional procedures under annealed conditions.
Welding
S2 tool steels are readily weldable using standard methods.
Heat Treatment
S2 tool steels are slowly preheated to 649ºC (1200ºF) and then directly heated by increasing the temperature to 871ºC (1600ºF). This is followed by holding the steels for 10 to 20 mins and quenching in brine or water.
Forging
Forging is carried out in S2 tool steels at temperatures ranging from 899 to 1093ºC (1650 to 2000ºF). Forging below 871ºC (1600ºF) is not preferred.
Cold Working
S2 tool steels can be cold worked under annealed conditions.
Annealing
Annealing is performed on S2 tool steels at 788ºC (1450ºF) followed by cooling in the furnace at a rate of not more than 4ºC per hour.
Tempering
S2 tool steels are tempered at 177 to 427ºC (350 to 800ºF) to obtain Rockwell C hardness of 60 to 50.
Shock resisting steels are designed to have high impact resistance (toughness), along with other properties such as strength, hardness. Silicon is a common addition to this class of steels, as it provides tempering resistance, and increases toughness.
Applications for shock resisting steels includes springs, as well as chisels, dies for forging, and punches. They are also used for screwdrivers and driver bits.
Type | C % | Si % | V % | Cr % | Mn % | Ni % | Mo % | W % |
S1 (UNS T41901) | 0.40-0.55 | 0.15-1.20 | 0.15-0.30 | 1.00-1.80 | 0.10-0.40 | <0.30 | <0.50 | 1.50-3.00 |
S2 (UNS T41902) | 0.40-0.55 | 0.90-1.20 | <0.50 | – | 0.30-0.50 | <0.30 | 0.30-0.60 | – |
S3 | 0.50 | 2.00 | – | 0.74 | – | – | – | 1.00 |
S4 (UNS T41904) | 0.4-0.65 | 1.75-2.25 | 0.35 | 0.35 | 0.60-0.90 | – | ||
S5 (UNS T41905) | 0.50-0.65 | 1.75-2.25 | <0.35 | <0.50 | 0.60-1.00 | – | 0.20-1.35 | – |
S6 (UNS T41906) | 0.40-0.50 | 2.00-2.50 | 0.20-0.40 | 1.20-1.50 | 1.20-1.50 | – | 0.30-0.50 | – |
S7 (UNS T41907) | 0.45-0.55 | 0.20-1.00 | 0.20-0.30 | 3.00-3.50 | 0.20-0.90 | – | 1.30-1.80 | – |
S2 and S7
Because the chemical compositions of S2 and S7 tool steel are similar, they respond similarly to most applications. For example, they are both hard to grind when compared to steel. S2, because of the slightly higher concentration of vanadium, S7 because of chromium addition.
AISI S2 is a Shock-Resisting Steel grade Tool Steel. It is composed of (in weight percentage) 0.40-0.55% Carbon (C), 0.30-0.50% Manganese (Mn), 0.90-1.20% Silicon (Si), 0.30% Nickel (Ni), 0.30-0.60% Molybdenum (Mo), 0.50% Vanadium (V), 0.25% Copper (Cu), 0.03% Phosphorus (P), 0.03% Sulfur (S), and the base metal Iron (Fe). Other designations of AISI S2 tool steel include UNS T41902 and AISI S2.Steel is the common name for a large family of iron alloys. Steels can either be cast directly to shape, or into ingots which are reheated and hot worked into a wrought shape by forging, extrusion, rolling, or other processes. Wrought steels are the most common engineering material used, and come in a variety of forms with different finishes and properties. Tool steels typically have excess carbides (carbon alloys) which make them hard and wear-resistant. Most tool steels are used in a heat-treated state, generally hardened and tempered.
The typical elastic modulus of tool steels at room temperature (25°C) ranges from 190 to 210 GPa. The typical density of tool steels ranges from 7.72 to 8.0 g/cm3. The typical tensile strength varies between 640 and 2000 MPa. The wide range of ultimate tensile strength is largely due to different heat treatment conditions.
Hardened SAE-AISI S2 is SAE-AISI S2 steel in the hardened (H) condition. The graph bars on the material properties cards below compare hardened SAE-AISI S2 to: tool steels (top), all iron alloys (middle), and the entire database (bottom). A full bar means this is the highest value in the relevant set. A half-full bar means it’s 50% of the highest, and so on. SAE-AISI S2 steel is a tool steel. S2 is the designation in both the SAE and AISI systems for this material. T41902 is the UNS number.
The properties of SAE-AISI S2 steel include two common variations. This page shows summary ranges across both of them. For more specific values, follow the links immediately below. The graph bars on the material properties cards further below compare SAE-AISI S2 steel to: tool steels (top), all iron alloys (middle), and the entire database (bottom). A full bar means this is the highest value in the relevant set. A half-full bar means it’s 50% of the highest, and so on.