AISI 1075 Spring Steel
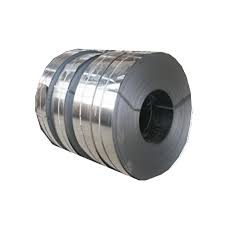
AISI 1075 Carbon Steel (UNS G10750)
Introduction
Carbon steels contain carbon as the chief alloying element. Residual elements such as copper, chromium, molybdenum, nickel, and aluminium are also present in traces. They also contain 1.2% of manganese and 0.4% of silicon. AISI 1075 carbon steel is more brittle than the lower carbon steels.
The following datasheet gives an overview of AISI 1075 carbon steel
Chemical Composition
The chemical composition of AISI 1075 carbon steel is tabulated below.
Element | Content (%) |
Iron, Fe | 98 |
Carbon, C | 0.70-0.80 |
Manganese, Mn | 0.40-0.70 |
Sulfur, S | 0.05 (max) |
Phosphorous, P | 0.04 (max) |
Physical Properties
The following table shows the physical properties of AISI 1075 carbon steel.
Properties | Metric | Imperial |
Density | 7.7-8.03 g/cm3 | 0.278- 0.290 lb/in3 |
Melting point | 1515°C | 2760°F |
Physical Data :
Density (lb / cu. in.) | 0.284 |
Specific Gravity | 7.86 |
Specific Heat (Btu/lb/Deg F – [32-212 Deg F]) | 0.107 |
Melting Point (Deg F) | 2760 |
Poissons Ratio | 0.3 |
Thermal Conductivity | 360 |
Mean Coeff Thermal Expansion | 6.7 |
Modulus of Elasticity Tension | 30 |
Modulus of Elasticity Torsion | 11 |
Mechanical Properties
The mechanical properties of AISI 1075 carbon steel are outlined in the following table.
Properties | Metric | Imperial |
Elastic modulus | 190-210 GPa | 27557-30458 ksi |
Poisson’s ratio | 0.27-0.30 | 0.27-0.30 |
Other Designations
Other designations that are equivalent to AISI 1075 carbon steel include:
ASTM A29 (1075)
ASTM A510 (1075)
ASTM A713 (1075)
SAE J403 (1075)
SAE J412 (1075)
Fabrication and Heat Treatment
Machinability
The machinability rate of AISI 1075 carbon steel is 50.
Forming
AISI 1075 carbon steel can be formed using conventional techniques.
Welding
AISI 1075 carbon steel can be welded using all welding methods. It is pre-heated at 260 to 315°C (500 to 600°F) and post-heated at 649 to 788°C (1200 to 1450°F) to prevent cracking.
Heat Treatment
AISI 1075 carbon steel can be hardened at 899°C (1650°F). It is then quenched in oil followed by tempering.
Forging
AISI 1075 carbon steel can be forged at 927 to 1204°C (1700 to 2200°F) followed by annealing.
Hot Working
AISI 1075 carbon steel can be hot worked at 94 to 483°C (200 to 900°F).
Cold Working
Cold working of AISI 1075 carbon steel is performed using conventional methods in the annealed condition. It needs more force compared to low carbon steels to perform this process.
Annealing
Annealing of AISI 1075 carbon steel can be done at 926°C (1700°F) followed by slowly cooling in the furnace.
Tempering
AISI 1075 carbon steel is tempered at 371 to 705°C (700 to 1300°F) after heating and quenching. It is usually used in the hardened condition of Rockwell C 55.
Hardening
AISI 1075 carbon steel is hardened by cold working, heating, and quenching.
Applications
AISI 1075 carbon steel is mainly used in cutting tools, and springs. Both metals are used to create many of the same products. The decision of which type to use in manufacturing depends upon your manufacturing process and the unique properties you would like the final product to have. Both 1075 and 1095 spring steel are used to make:
Vehicle Coil Springs
Spring Clamps
Antennas
S-Tines
Lock Picks
Clock Hands
STANDARD SPECIFICATIONS: ASTM A684-17
TYPICAL ANALYSIS: C .69/.80 Mn .40/.80 P .020 max. S .025 max Si.15/.30
TYPICAL HARDNESS: Cold Rolled, Spherically annealed, RB 85
TYPICAL APPLICATIONS: Blades, brackets, clutches, hand tools, springs, scrapers, washers, & wear strips
XC75 steel is perfect for beginners starting to make knives.
The XC 75 carbon steel is also called 1075 in the USA and is the ideal grade to use for beginners. It provides excellent value for money and creates good quality blades at a very reasonable price.
Ideal for forging Damascus blades.
The XC75 steel has little or no alloy, and is very easy to weld. Combined with 15N20, which has the same carbon content – or may contain pure nickel for a more brilliant white finish – it can be used to obtain very attractive patterns whilst conserving very good cutting properties