EN24 and EN24T Steel
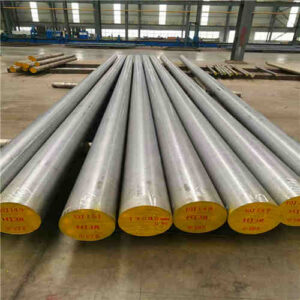
EN24 and EN24T Steel
EN24 is usually supplied in the finally heat treated condition (quenched and tempered to “T” properties) up to a limiting ruling section of 250mm, which is superior to grades 605M36, 708M40 or 709M40 – see properties below. Please refer to our selection guide for comparisons.
In addition to the above, EN24T is capable of retaining good impact values at low temperatures, hence it is frequently specified for harsh offshore applications such as hydraulic bolt tensioners and shipborne mechanical handling equipment.
817M40 (EN24) Specification Chemical composition |
|
Carbon | 0.36-0.44% |
Silicon | 0.10-0.35% |
Manganese | 0.45-0.70% |
Sulphur | 0.040 Max |
Phosphorus | 0.035 Max |
Chromium | 1.00-1.40% |
Molybdenum | 0.20-0.35% |
Nickel | 1.30-1.70% |
EN24 is a very high strength steel alloy which is supplied hardened and tempered.
817M40 (EN24) – mechanical properties in “T” condition | ||
Max Stress | 850-1000 n/mm2 | |
Yield Stress | 680 n/mm2 Min | (up to 150mm LRS) |
Yield Stress | 650 n/mm2 Min | (over 150 to 250mm LRS) |
0.2% Proof Stress | 665 n/mm2 Min | (up to 150mm LRS) |
0.2% Proof Stress | 635 n/mm2 Min | (over 150 to 250mm LRS) |
Elongation | 13% Min | (9% if cold drawn) |
Impact KCV | 50 Joules Min | (up to 150mm LRS |
Impact KCV | 35 Joules Min | (over 150 to 250mm LRS) |
Hardness | 248-302 Brinell | (850-1000 n/mm2) |
EN24 Equivalents | |
BS970: 1955 | EN24 |
BS970/PD970: 1970 onwards |
817M40 |
European | 34CrNiMo6 |
Werkstoff No. | 1.6582 |
US SAE (AISI) | 4340 |
EN24 STEEL Delivery Condition
1.Shape:Round/Square / Flat/Shafts/Rollers/Blocks
2.Surface condition:Black surface/Bright surface
3.Heat Treatment:Normalized/Annealed/QT
4.Straightness:Max 3mm/m(Enhanced straightness may be available on request)
5.Length:3000-5800mm suitable for 20″container. above 6000mm,suitable for 40″ container
6.Grain Size: 5-8 acc to ASTM E112-96
7.Typcial Hardness:HRC28-32
8.Ultrasonic Standard: Sep1921/ASTM A388/EN 10228-3
9.Non Metallic Inclusion: 2 max acc to ASTM E45 /K4≤20 acc to DIN 50602
10.Forging Ratio: minimum 4 : 1
11.Marking: Grade/Weight/Length/Size/Heat Number
EN24 STEEL Heat Treatment
Soft annealing °C | Cooling | Hardness HB |
650-700 | slowly | max. 280 |
Stress-relief annealing °C | Cooling |
630 – 650 | Furnace |
1st pre-heating °C | 2nd and 3rd | Hardening °C | Quenching | Tempering °C | Hardness after Teperature HRC |
up to approx. 400 in an air-circulating furnace | 780 and 1000 | 1190 – 1230 | Saltbath, at least 520 °C Oil ,Air | at least twice 530-560 | 64 – 66 |
EN24 STEEL Chemical Composition
EN24 steel (En24T steel) and BS970 817M40 material chemical composition is listed in the following table.
Chemical Composition (Cast Analyses ), % | ||||||||||
Country (Region) | Standard | Steel Grade | C | Si | Mn | P, ≤ | S, ≤ | Cr | Ni | Mo |
Britain | BS 970-1955 | En24 (En24T) | 0.35-0.45 | 0.10-0.35 | 0.45-0.70 | 0.050 | 0.05 | 0.90-1.40 | 1.3-1.8 | 0.20-0.35 |
BS 970-1991 | 817M40 | 0.36-0.44 | 0.10-0.40 | 0.45-0.70 | 0.035 | 0.04 | 1.00-1.40 | 1.3-1.7 | 0.20-0.35 |
EN24 STEEL Mechanical Properties
En24 (En24T) and 817M40 steel mechanical properties are listed in the following tables including yield strength (yield stress), ultimate tensile strength, shear strength, modulus of elasticity, young’s modulus, etc.
Notes:
1 MPa = 1 N/mm2
1 GPa = 1 kN/mm2
Reference symbols for tensile strength ranges | |
Symbol | Tensile Strength, MPa (ksi) |
P | 550-700 (80-100) |
Q | 625-775 (90-112) |
R | 700-850 (100-123) |
S | 775-925 (110-134) |
T | 850-1000 (123-145) |
U | 925-1075 (134-156) |
V | 1000-1150 (145-167) |
W | 1075-1225 (156-177) |
X | 1150-1300 (167-188) |
Y | 1225-1375 (177-199) |
Z | ≥ 1550 (225) |
En24T, En24 Mechanical Properties | ||||||||
Standard | Steel | Hardened and tempered condition | Limiting ruling section, in (mm) | Tensile strength, tons/in2 (Mpa) [ksi], ≥ | Yield stress, tons/in2 (Mpa) [ksi], ≥ | Elongation, %, ≥ | Izod impact, ft lb, ≥ | Brinell hardness, HB |
BS970-1955 | En24 | S | 6 (152) | 50 (772) [112] | 38 (587) [85] | 20 | 40 | 223-277 |
T | 6 (152) | 55 (850) [123] | 44 (680) [98] | 18 | 40 | 248-302 | ||
U | 4 (101) | 60 (926) [134] | 48 (741) [107] | 17 | 35 | 269-321 | ||
V | 2.5 (63.5) | 65 (104) [145] | 52 (803) [116] | 16 | 35 | 293-341 | ||
W | 1.125 (28.5) | 70 (1081) [157] | 58 (895) [130] | 15 | 30 | 311-375 | ||
X | 1.125 (28.5) | 75 (1158) [168] | 63 (973) [141] | 14 | 25 | 341-388 | ||
Y | 1.125 (28.5) | 80 (1235) [179] | 68 (1050) [152] | 14 | 22 | 363-415 | ||
Z | 1.125 (28.5) | 100 (1544) [224] | 85 (1313) [190] | 8 | 8 | ≥ 444 |
BS970 817M40 Steel Mechanical Properties | |||||||||
Standard | Steel | Tensile strength, Mpa (ksi), ≥ | Yield strength, Mpa (ksi), ≥ | 0,2 % proof strength | Elongation after fracture, 5.65 √S0 , ≥ | Impact, Izod (Charpy V-notch impac) in J, ≥ | Hardness, HB | Diameter across flats or thickness (t), mm | Condition |
BS 970-1991 | 817M40 | 850-1000 (123-145) | 650 (94) | 635 (92) | 13 | 40 (35) | 248-302 | 150<t≤250 | Normalized + turned or ground |
850-1000 (123-145) | 680 (98) | 665 (96) | 13 | 54 (50) | 248-302 | 63<t≤150 | |||
925-1075 (134-156) | 750 (109) | 740 (107) | 12 | 47 (42) | 269-331 | 29<t≤100 | |||
1000-1150 (145-166) | 850 (123) | 835 (121) | 12 | 47 (42) | 293-352 | 13<t≤63 | |||
1075-1225 (156-177) | 940 (136) | 925 (134) | 11 | 40 (35) | 311-375 | 6≤t≤29 | |||
1150-1300 (166-188) | 1020 (145) | 1005 (145) | 10 | 34 (28) | 341-401 | 6≤t≤29 | |||
≥ 1550 (225) | 1235 (179) | 1125 (163) | 5 | 10 (9) | 444 ≥ | 6≤t≤29 | |||
850-1000 (123-145) | 700 (101) | 680 (98) | 9 | 54 (-) | 248-302 | 63<t≤150 | Hardened and tempered + cold drawn or hardened and tempered + cold drawn + ground |
||
925-1075 (134-156) | 770 (111) | 755 (109) | 9 | 47 (-) | 269-331 | 29<t≤100 | |||
1000-1150 (145-166) | 865 (125) | 850 (123) | 9 | 47 (-) | 293-352 | 13<t≤63 | |||
1075-1225 (156-177) | 955 (138) | 940 (136) | 8 | 40 (-) | 311-375 | 6≤t≤29 | |||
1150-1300 (166-188) | 1035 (150) | 1020 (150) | 7 | 34 (-) | 341-401 | 6≤t≤29 | |||
≥ 1550 (225) | 1250 (181) | 1235 (179) | 3 | 11 (-) | ≤ 444 | 6≤t≤29 | |||
227 | Turned, ground or cold drawn and finally softened |
EN24 STEEL Heat Treatment
En24 material heat treatment are listed below, including normalizing, hardening and termpering.
Hardening: 830 to 860 °C (1525-1580 °F), oil quench,
Tempering temperature: 550 to 660 °C (1020-1220 °F)
En24 Steel Equivalent Grade
BS970 817M40 material or En24T, En24 steel equivalent to European EN (German DIN EN, French NF EN), ISO, Japanese JIS and Chinese GB standard (for reference).
En24T, En24 and 817M40 Steel Equivalent | |||||||||||
Britain | European Union | ISO | China | US | Japan | ||||||
Standard | Steel name | Standard | Steel name (Steel number) | Standard | Grade | Standard | Grade | Standard | Grade (UNS) | Standard | Grade |
BS970-1955; BS970-1991 |
En24; 817M40 |
EN 10083-3 | 34CrNiMo6 (1.6582) | ISO 683-18 | 34CrNiMo6 | GB/T 3077 | 34Cr2Ni2Mo |
EN24 is a very popular grade of through-hardening alloy steel, which is readily machinable in the “T” condition. (Refer to our machinability guide). EN24T is most suitable for the manufacture of parts such as heavy-duty axles and shafts, gears, bolts and studs. EN24T can be further surface-hardened typically to 58-60 HRC by induction or nitride processes, producing components with enhanced wear resistance.
EN24 sections larger than 250mm may still be available in the quenched and tempered condition, but it should be noted that a fall-off in mechanical properties may be apparent approaching the centre of the bar.
It is therefore recommended that larger sizes are supplied in the annealed (softened) condition, and that quenching and tempering is carried out after initial stock removal. This should achieve better mechanical properties towards the core.
EN24 STEEL VERY HIGH STRENGTH
The grade is a nickel chromium molybdenum combination – this offers high tensile steel strength, with good ductility and wear resistance characteristics. With relatively good impact properties at low temperatures, EN24 is also suitable for a variety of elevated temperature applications.
EN24 STEEL SUITABILITY
EN24 engineering steel is easy to treat and temper and is supplied hardened and tempered. The alloy offers a good combination of strength, ductility and wear resistance. It is a very high strength alloy engineering steel.
EN24 STEEL TYPICAL APPLICATIONS
For all metal-cutting tools for roughing or finishing such as twist drills, diverse milling cutters, thread dies, broaches, reamers, countersinks, thread chasers, circular saw segments, shaping tools and woodworking tools. Also highly suitable for cold-forming tools such as cold extrusion rams and dies, as well as cutting and precision cutting tools, plastic moulds with elevated wear resistance and screws.Commercial applications for this engineering material include:
High strength shafts
Punches & dies
Drill bushings
Retaining rings
Gears
EN24 Steel Quality Certification
A material test report(Inspection Certificate EN 10204 3.1) will be provided, documenting the following:
1.Chemical analysis
2.Mechanical properties
3.Surface hardness
4.Non Metallic Inclusion
5.Heat Treatment Process
6.Grain size
7.Forging ratio
8.NDE test method/criteria