D7 Tool Steel
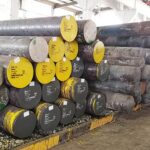
D7 Tool Steel
D7 tool steel is a high-carbon, high-chromium air-hardening tool steel that exhibits exceptional wear resistance. The high carbon and vanadium contents result in numerous, hard vanadium carbide particles in the steel. These carbides exhibit a hardness that is equivalent to approximately 80 to 85 Rockwell C.
The following are the list of applications of D7 tool steels:
- Brick mold liners
- Powder compaction tooling
- Shot blasting equipment liners
- Flattening rolls
- Powder compaction tooling
- Tools for ceramic extrusion and molding.
Designations:
ASTM A681-US
FED QQ-T-570-US
SAE J437-US
SAE J438-US
UNS T30407-US
AISI D7 Tool Steel-US
Chemical composition(mass fraction)(wt.%) of the D7
C(%) | Si(%) | Mn(%) | P(%) | S(%) | Cr(%) | Mo(%) | V(%) |
2.15~2.50 | 0.10~0.60 | 0.10~0.60 | ≤0.030 | ≤0.030 | 11.5~13.5 | 0.70~1.20 | 3.80~4.40 |
Smelting Option
1 EAF: Electric Arc Furnace
2 EAF+LF+VD: Refined-smelting and vacuum degassing
3 EAF+ESR: Electro Slag Remelting
4 EAF+PESR: protective atmosphere Electro Slag Remelting
5 VIM+PESR: Vacuum induction melting
Forming Option
1 Hot rolling process
2 Hot Forging: Electro-hydraulic; High-speed-hydraulic; Oil-hydraulic; Precision-forging
Heat-treatment Option
1 +A: Annealed (full/soft/spheroidizing)
2 +N: Normalized
3 +NT: Normalized and tempered
4 +QT: Quenched and tempered (water/oil)
Suface Option
1 Black Surface
2 Grounded: Bright but rough ; Not precision
3 Machining for plate: Bright and precision; Little turning scar
4 Peeled/Turned: Bright and precision; Little turning scar
5 Polished: Very Bright and precision size; Not turning scar
Other Services
1 Cutting: Small pieces
2 CNC Machine: Produce as your drawing
3 Package: Bare/Nylon/Canvas/Wooden
4 Payment:T/T, L/C, O/A(request credit)
5 Transport:FOB/CFR/CIF/DDU/DDP (train/ship/Air)
MECHANICAL PROPERTIES
Yield Rp0.2 (MPa) |
Tensile Rm (MPa) |
Impact KV/Ku (J) |
Elongation A (%) |
Reduction in cross section on fracture Z (%) |
As-Heat-Treated Condition | Brinell hardness (HBW) |
984 (≥) | 682 (≥) | 41 | 31 | 23 | Solution and Aging, Annealing, Ausaging, Q+T,etc | 322 |
Forging/Rolling:
Preheat to 1500° F and soak thoroughly. Then raise to 2050° F – 2125° F. Do not forge or roll below 1800° F, cool slowly from the forging or rolling temperature. Do not normalize.
Annealing:
Heat slowly to 1600° F – 1650° F, and hold for uniformity, furnace cool at a rate of 20° F per hour to 1000° F then air cool. Expect Brinell hardness 235 – 262.
Hardening:
Preheat to 1500° F and soak until uniformly heated and either transfer or raise furnace temperature to 1850° F – 1950° F, and hold 1 hour per inch of greatest thickness. Cool in still air.
Tempering:
Temper immediately after quenching, before part has cooled to below 150° F. Parts should be held a minimum of 2 hours per inch of greatest thickness. Double tempering is recommended. For maximum wear resistance temper at 300° F. The above tempering table may be used as a guide. However, since 1/2″ dia. specimens were used for this test, it may be found that heavier sections are several points lower.