1.2885 X32CrMoCoV3-3-3 H10A Hot Working Tool Steel
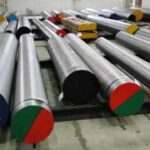
1.2885 X32CrMoCoV3-3-3 H10A Hot Working Tool Steel
X32CrMoCoV3-3-3 1.2885 Alloy tool steel with high hardenability, high resistance to tempering, load and high hardness at elevated temperatures. The grade is distinguished by high content of Cobalt in its chemical composition.
Applications
Hot pressing tools exposed to severe stresses in contact with the die insert-mandrels,stamps, punching tools,dies,etc.
Designation by Standards
Steel No. :1.2885
DIN EN :X32CrMoCoV3-3-3
AISI :H10A
Chemical composition (wt.%)
C(%) | Si(%) | Mn(%) | P(%) | S(%) | Cr(%) | Mo(%) | V(%) | Co(%) |
0.28-0.35 | 0.10-0.40 | 0.15-0.45 | Max 0.030 | Max 0.030 | 2.70-3.20 | 2.60-3.00 | 0.40-0.70 | 9.50-10.5 |
Smelting Option
1 EAF: Electric Arc Furnace
2 EAF+LF+VD: Refined-smelting and vacuum degassing
3 EAF+ESR: Electro Slag Remelting
4 EAF+PESR: protective atmosphere Electro Slag Remelting
5 VIM+PESR: Vacuum induction melting
Forming Option
1 Hot rolling process
2 Hot Forging: Electro-hydraulic; High-speed-hydraulic; Oil-hydraulic; Precision-forging
Heat-treatment Option
1 +A: Annealed (full/soft/spheroidizing)
2 +N: Normalized
3 +NT: Normalized and tempered
4 +QT: Quenched and tempered (water/oil)
Suface Option
1 Black Surface
2 Grounded: Bright but rough ; Not precision
3 Machining for plate: Bright and precision; Little turning scar
4 Peeled/Turned: Bright and precision; Little turning scar
5 Polished: Very Bright and precision size; Not turning scar
Other Services
1 Cutting: Small pieces
2 CNC Machine: Produce as your drawing
3 Package: Bare/Nylon/Canvas/Wooden
4 Payment:T/T, L/C, O/A(request credit)
5 Transport:FOB/CFR/CIF/DDU/DDP (train/ship/Air)
Mechanical properties of 1.2885, X32CrMoCoV3-3-3
Hardness in softening annealed condition <241 HB
Hardness after hardening 53.5 HRC
Hardness after tempering at temperature:
- 300C = 51.5 HRC
- 350C = 51.5 HRC
- 400C = 52.0 HRC
- 450C = 52.5 HRC
- 500C = 53.0 HRC
- 550C = 53.5 HRC
- 600C = 51.5 HRC
Heat treatment – processes and temperatures:
Softening annealing at 740 – 770C with cooling in furnace
Relief annealing at a temperature of 600 – 700C with cooling in furnace
Nitriding at a temperature of 470 – 550C
Hardening at a temperature of 1020 – 1040C with cooling in oil
Tempering at a temperature of 500 – 600C