1.2764 X19NiCrMo4 Tool Steel For Plastic Mould
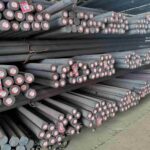
1.2764 X19NiCrMo4 Tool Steel For Plastic Mould
1.2764 X19NiCrMo4 is Case hardening steel,when hardened high core strength,good polishability in hardened condition.
Applications:
Press tools,highly stressed plastic moulds,profiling rolls.
Condition of delivery:
Soft annealed to max.250 HB
Chemical composition(mass fraction)(wt.%)
Elements | Min.(≥) | Max.(≤) |
C | 0.16 | 0.22 |
Si | 0.10 | 0.40 |
Mn | 0.15 | 0.45 |
P | 0.030 | |
S | 0.030 | |
Cr | 1.10 | 1.40 |
Mo | 0.15 | 0.25 |
Ni | 3.80 | 4.30 |
W | 0.30 | 0.50 |
Smelting Option
1 EAF: Electric Arc Furnace
2 EAF+LF+VD: Refined-smelting and vacuum degassing
3 EAF+ESR: Electro Slag Remelting
4 EAF+PESR: protective atmosphere Electro Slag Remelting
5 VIM+PESR: Vacuum induction melting
Forming Option
1 Hot rolling process
2 Hot Forging: Electro-hydraulic; High-speed-hydraulic; Oil-hydraulic; Precision-forging
Heat-treatment Option
1 +A: Annealed (full/soft/spheroidizing)
2 +N: Normalized
3 +NT: Normalized and tempered
4 +QT: Quenched and tempered (water/oil)
Suface Option
1 Black Surface
2 Grounded: Bright but rough ; Not precision
3 Machining for plate: Bright and precision; Little turning scar
4 Peeled/Turned: Bright and precision; Little turning scar
5 Polished: Very Bright and precision size; Not turning scar
Other Services
1 Cutting: Small pieces
2 CNC Machine: Produce as your drawing
3 Package: Bare/Nylon/Canvas/Wooden
4 Payment:T/T, L/C, O/A(request credit)
5 Transport:FOB/CFR/CIF/DDU/DDP (train/ship/Air)
Mechanical properties of grade 1.2764
Yield Rp0.2 (MPa) |
Tensile Rm (MPa) |
Impact KV (J) |
Elongation A (%) |
Reduction in cross section on fracture Z (%) |
As-Heat-Treated Condition | HBW |
373 (≥) | 646 (≥) | 22 | 33 | 33 | Solution and Aging, Annealing, Ausaging, Q+T,etc | 233 |
Physical properties(average values)at ambient temperature
Modulus of elasticity[103x N/mm-]:210
Density [g/cm3]:7.80
Soft Annealing
Heat to 620-660C,cool slowly in furnace.This will produce a maximum Brinell hardness of 255.
Intermediate Annealing
Temperature:600-630C.
Carburizing
Temperature:860-890C.
Hardening
Harden from a temperature of 780-810C followed by oil quenching or thermal bath at 180- 220C.
Tempering
Tempering temperature:150-180C.
Forging
Hot forming temperature:1050-850c.