Linear Guide
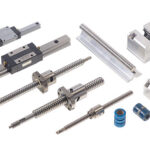
Linear Guide
Linear Guide overview
Linear Guides are a block and rail system that helps support the motion of an application.
Linear Guideways
- A four row ball system provides a high load rated linear guideway.
- The two point ball contact characteristics of the circular arch raceways ensure very low friction.
- The guideway options are either the international or compact version, with a long or short trolley, and with or without flanges.
- Precision classes and preload options are available.
- Guide rail up to 4000mm in length.
Shafts, Shaft Supports & Shaft Blocks
- Shafts are hardened and ground and available from 5mm to 100mm in diameter.
- Induction hardened steel + hard chrome + rust resistant and stainless-steel shafting is available with fixing holes and ends machines, as required.
- Lengths up to 7800mm available.
- Shaft supports and blocks determine the position of the guide shafts.
- Flat + low profile alloy + low profile steel + medium height alloy + medium height alloy extrusion and full height are the types of shaft support available, all with fixing hole options.
- Standard lengths for machined supports are 600mm and 6000mm for extruded supports.
- Shaft blocks are available for single or twin shaft assemblies.
How linear Guides Work
There are two parts to the Linear Guide System: the Linear Block and the Linear Rail. The linear block moves along the linear rail along the plane the rail is positioned for. The block moves forward and backward along the straight linear rail. Linear blocks connect to the moving components by mounting to the block to support the motion for the specified component. The motion is created along the rail through recirculating ball bearings within the block that is contacted on the rail.
Basic Types of Linear Guides
Two basic types of linear guides are predominantly used in industry today. These types are: sliding contact linear motion bearing and rolling element linear motion bearing guides. The main distinction between the two is how the motion of the linear block occurs along the linear rail.

Linear roller guide rail

ball screw

ball spline
Sliding contact
The sliding contact is considered the oldest type of linear guide used within industry. This may be because of its simplicity and low in manufacturing that companies still use this “old technology.” A huge drawback with the sliding contact is its high coefficient of friction compared to its other types. With such a high coefficient of friction it becomes difficult for companies to use this type of guide for applications with high precision or high speed. This huge setback makes it hard to predict and design an exact lifetime for the linear guides.
Rolling Element
This type of linear guide is known to be the most commonly used type for most applications. Ball bearings, or rollers, are elements usually used within these blocks to create the rolling motion of the block. The coefficient of friction is therefore already decreased from the original sliding contact block just because of the rolling action. These types of blocks are easier to control increasing accuracy, precision, and speed for the guide. There are a wide variety of options to customize this block, another reason why it is generally a better choice over the sliding contact block.
Industries that Use Linear Guides
A wide variety of industries use and order linear guides for their own applications. Linear guides are used to move a machine table in either the X or Y direction. Applications which require high precision use linear guides due to their high accuracy and precision capabilities. In the application to the left, each table uses linear guides for positioning. Machine tool applications use linear guides because of their ability to manage temperature rise and high speed changes. Linear guides are used to transport heavy product with ease. In this application, the linear guides were used to help create the motion of a robot pick-and-place machine.
Troubleshooting a Linear Guide
There are a few things to look for in your linear guide that want to avoid. Regularly machinery such as corrosion of the rail, indentations in the rail, or wear can occur within the linear guide. These different damages can occur because of poor care of the system, excessive misalignment, contaminating the rail with the wrong product, or poor lubrication. An easy way to troubleshoot these types of problems is to always clean and care for the blocks and the rails, and make sure the installation is followed as stated in the manuals.
The Cost of Linear Guides
The cost of linear guides is dependent upon size and material of the linear guides. For applications with higher load capacity, you will generally need a bigger linear block. In this case the wider the block or the longer the rail needed will increase the price of the linear guide. For more specific pricing inquiries please contact the factory to assist you in pricing.
Required Maintenance for a Linear Guide
Most linear guides are equipped with a lubrication mechanism within the block. This is a great advantage because it essentially decreases the maintenance required for the user of linear guide. The main requirement is to just refill the grease lubrication when needed and the block will have a longer lifetime. Although the lubrication does help decrease maintenance, linear guides still need to be dusted and cleaned from unwanted debris that would cause the linear guide to deteriorate.
Environmental Aspects for a Linear Guide
The environment of a linear guide in use is dependent upon the application of the linear guide. Certain precautions should be taken for different environments. Linear Guides should have a clean, debris free environment because of its re-circulating rolling elements. These rolling elements may lose its lubrication when interfering with dirt on the rail. Although a clean environment cannot be sustained in some applications at all times, an upgraded lubrication option can be added to a linear guide to help increase lifetime of the guide in a dirtier environment.
Accuracy
Based on the running accuracy of ball slides that travel on the rails, the required motion accuracy is expressed in a particular accuracy grade, like P5 or PN.
Applied Loads
These are the loads applied to the linear guides, which usually consist of self-weight of a table, weight of transported objects, and/or forces that are working on a machine tool. The loads are normally applied vertically or laterally against motion axis.
Application
This is the information on the type of machine (application) like machine tools, transporting systems, or measurement apparatuses for which linear guides are to be used. Generally, such information is very useful to select the appropriate linear guides.
Ball Bearings
Steel circular balls that create the motion for the linear guide system through its re-circulation.
Dynamic Load Capacity
The amount of force the linear guide can withstand when the block is in motion.
Grease
The class of lubricants applied to smooth the movement of guides and moving parts of the ball screw. Grease forms an oil film on metal surface to reduce wear and friction, thereby prolonging the life and preventing rust. Linear slides require periodic maintenance of grease according to their use conditions.
Linear Guide Block
The block that moves along the track that supports the machine or application it is holding. It houses the lubrication and the re-circulating bearings within the block.
Linear Guide Rail
The track that the block moves on made of carbon steel. This track is a uniaxial track, meaning it travels only along one axis.
Load Moment
When the load acting upon the table extends beyond the table in the longitudinal, lateral or vertical direction, the linear slide receives a torsional force.
Machine Structure
This information covers the structure of machines and their relevant aspects of construction such as dimensions around the place where linear guides are mounted to, positions and directions of external forces, etc. This is compulsory information for selecting particular linear guides.
Pitch
The hole-to-hole distances found on the linear rails.
Required Life
Required life is expressed in a total travel distance (For example, 5000 km).
Service Life
The calculated time the linear guide can withstand before failure in hours.
Speed
This means a relative speed of the table (with the ball slides) against the rails. It is expressed as, for example, 100 m/min.
Static Load Capacity
The amount of force the linear guide can withstand when the block is not moving.
Stroke
This means a travel distance that a table mounted on ball slides is required to make.