1.2162 21MnCr5 20ХГ Cold Work Tool Steel
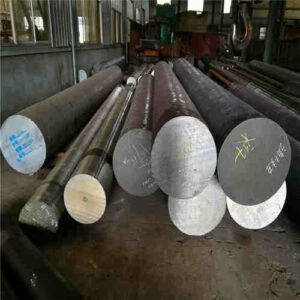
1.2162 21MnCr5 20ХГ Cold Work Tool Steel
Grade : 21MnCr5 Number: 1.2162
Classification
Alloy cold-work tool steel
Standard:
EN ISO 4957: 2000 Tool steels
Characteristics
Manganese-chrome steel for case-hardening with the middle hardenability, with the hardness of case-hardened layer and with the high hardness in the core. Further the steel is characterized by a good ductility at the heat, good workability in the annealed state and it is easy to polish.
APPLICATION:
machine parts and moulding plates with a high surface hardness;
synthetic resin press moulds for the processing of thermoplastics and thermosetting plastics.
Suitability
For small and middle-size cemented molds for mechanical working of plastic materials and rubber with the demand on higher hardness in the core.
Chemical composition%of the ladle analysis of grade 1.2162
C(%) Si(%) Mn(%) P(%) S(%) Cr(%)
0.18-0.24 0.15-0.35 1.10-1.40 Max 0.030 Max 0.030 1.00-1.30
Product range
Round bars: D10 – D615
Blocks: 510×1010
Metal sheets: s.5 – s.150
We will deliver any semi-finished products from the above mentioned dimensions. Other dimensions, except for given stock supplies, have to be consulted with us.
HEAT TREATMENT:
Soft annealing:
670 to 710 °C for about 2 to 5 hours
slow controlled cooling, further cooling in air, max. 205 HB
Carburising:
900 to 950 °C. The choice of the carburising means and carburising temperature depends on the desired surface carbon content, the carburising graph and the required case depth.
Application:
870 to 930 °C in powder/salt bath, cooling in oil/warm bath at 160 to 250 °C
Intermediate stress-relieving heat treatment:
630 to 650 °C, about 2 to 4 hours with slow furnace cooling
Preheating:
350 °C depending on dimensions
Hardening:
curing temperature 810 to 840 °C in oil of ~ 60 °C warmth
Cooling:
down to about 100 °C in oil, then in air to about 50 °C
Tempering:
1 hour per 20 mm part thickness, at least 2 hours