AISI A6 Tool Steel Bar
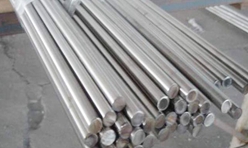
a6 steel tool steel
1 A6 Steel Introduction
A6 Tool Steel is an air hardening, cold work die steel which exhibits less distortion during heat treatment than water or oil hardening steels and most high alloy, air hardening die steels. It is a fully air hardening steel, A6 Tool Steel inch cube hardening to Rockwell C 60 in still air. In addition, A6 Tool Steel has the advantage of a low hardening temperature range, 1500′-1600F, usually available only in oil hardening steels.
2 A6 Steel Applications
Typical applications for A6 Tool Steel are blanking dies, forming dies, trim dies, stamping dies, coining dies, notching dies, bending tools, rim rolls, punches, cams, thread roll dies, spindles, retaining rings, master hobs, precision tools, mandrels, compression molds, plastic molds requiring high hardness, ball screws, lead screws, general purpose tooling, etc.
3 Quality Standard
: ASTM A681 – 08 Standard Specification for Tool Steels Alloy.
4 All Grades Comparison
ASTM | FED | UNS |
---|---|---|
A2 | QQ-T-570 | T30i06 |
5 A6 Steel Chemical Composition(%)
C | Si | Mn | P | S | Cr | Mo |
---|---|---|---|---|---|---|
0.65-0.75 | 0.10-0.70 | 1.80-2.50 | 0.030 max | 0.030 max | 0.90-1.40 | 0.90-1.40 |
6 HEAT TREATMENT
Forging:Heating for forging must be done slowly and uniformly. Soak through at 1900°-2000°F and reheat as often as necessary, stopping work when the temperature drops below 1600°F. After forging, cool slowly in lime, mica, dry ashes or furnace. A6 Tool Steel should always be annealed after forging.
Annealing:Heat slowly to 1350°-1375°F, hold until entire mass is heated through, and cool slowly in the furnace (20F per hour) to about 1000°F, after which cooling rate may be increased. Suitable precautions must be taken to prevent excessive carburization or decarburization.
Hardening:Parts at room temperature or as pre-heated should be placed in a hardening furnace operating at 1525°-1600°F. After parts have reached the furnace temperature, hold 20 minutes for small parts and up to 45 minutes for large parts.
Tempering:A single temper (one hour at temperature for small pieces; proportionately longer time for larger sizes) is usually all that is required with tempering carried out in the range of 300°-1000°F. For most applications, the best combination of hardness and toughness is accomplished at 350°-400°F. Specimens 1 inch square by 3 inches long were air hardened from 1550°F and tempered at various temperatures for two hours.
7 Mill′s test certificate
EN 10204/3.1 with all relevant data reg. chem. composition, mech. properties and results of testing.