AISI 9310 Alloy Steel
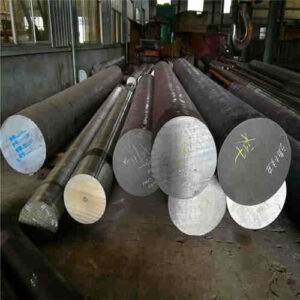
AISI 9310 Alloy Steel
ALLOY STEEL 9310 AMS 6265 VAR – UNS 93106
9310 is low alloy steel containing nickel, chromium and molybdenum. It has high core hardness and high fatigue strength. This alloy is best machined in the normalized and tempered state. All of this makes 9310 excellent for aircraft parts. 9310 steel specializes in high core strength applications. It also exhibits good strength, high toughness, hardenability, core strength, and very high fatigue strength. When annealed, 9310 has good ductility, machinability, and cold working properties. Additionally, 9310 is easily welded. It is typically used in gears, crankshafts, heavy-duty gears, the automotive, trucking, and aerospace industries.
9310 nickel-chrome-molybdenum low alloy steel is melted as AOD + VAR or VIM + VAR melt type. The alloy additions of nickel, chromium, and molybdenum help give this grade very good strength and toughness . This grade also has the ability to be case hardened making it an excellent candidate for heavy duty gears and shafts often used in the aircraft industry
GENERAL CHARACTERISTICS OF ALLOY STEEL 9310
This is a nickel-chrome-molybdenum case-hardening steel, with good strength and toughness properties. It shows high hardenability, high core hardness and high fatigue strength.
SPECS USAP PRODUCES TO:
AMS 6260
AMS 6265
AMS 6267
AMS STD 2154
BENEFITS OF 9310 steel
Normalized & Tempered
Solid strength and toughness properties
High Hardenability, High Core Hardness, and High Fatigue Strength
9310 steel is a low alloy steel that contains Nickel, Chromium, and Molybdenum. Alloy 9310 Bar is a triple alloy based on the inclusion of the previous elements of Nickel, Chromium, and Molybdenum.
9310 Vac Melt is a high quality carburizing steel produced by a vacuum consumable electrode process. 9310 has a high hardenability, high core hardness and high fatigue strength. All of those aspects considered, 9310 steel is ideally suited for aircraft engine gear and pinon applications.
9310 Alloy Steel is manufactured for the purpose of case hardening and 9310 steel is deep hardening. Generally 9310 steel is most commonly used in applications where toughness, high wear resistance and strength are required.
9310 VAR AMS 6265 is a Chromium-Nickel-Molybdenum Alloy used as a Carburizing Grade for Aircraft Parts. Users can obtain high case hardness coupled with high core strength and toughness. High alloy content makes it suitable for use in relatively large cross-sections. Its combination of high alloy and low carbon content can achieve high core hardness with a narrow range between thicker and thinner part cross sections.
This alloy can be used in some applications without case-hardening, as it exhibits strength with excellent toughness and ductility. Carburizing offers a highly wear-resistant surface. Service Steel Aerospace stocks Premium Aircraft Quality produced double melted in an Electric Furnace, followed by a VAR, or Vacuum Arc Remelt (also known as CEVM). Standard air-melted Aircraft Quality AMS 6260 Air Melt material is available on request. 9310 VIM-VAR material is also available on request.
APPLICATIONS OF 9310 STEEL
Components with large cross section requiring high toughness and core strength such as gears, crankshafts and heavy-duty gear shafts in aircraft and truck construction.
9310 VAR steel is typically used in the following applications:
Aircraft engine gears & pinions
Shafts
Clutch Parts
Boring bars
Piston pins
Aluminum rolling mill rolls
Symbol | Element | Min % | Max % |
C | Carbon | 0.07% | 0.13% |
Mn | Manganese | 0.40% | 0.70% |
Si | Silicon | 0.15% | 0.35% |
P | Phosphorus | 0.015% | |
S | Sulfur | 0.015% | |
Cr | Chromium | 1.00% | 1.40% |
Ni | Nickel | 3.00% | 3.50% |
Mo | Molybdenum | 0.08% | 0.15% |
B | Boron | 0.001% (10 ppm) | |
Cu | Copper | 0.035% |
AISI 9310 STEEL FORGING
This alloy would be forged between 2250 and 1700ºF (1230 and 925ºC.)
AISI 9310 STEEL HEAT TREATMENT
Annealing: Not normally annealed: if so sub-critical anneal to give spheroidized structure.
Normalizing: 1650-1700ºF (900-930ºC.)
Carburizing: 1650-1740ºF (900-950ºC) and oil quench.
Hardening: Core: 1530-1620ºF (830-880ºC) and oil quench. Case: 1440-1470ºF (780-800ºC ) and oil quench
Tempering: 340-410ºF (170-210ºC.)
Type | Process |
Annealing | Heat throughout to 1475° – 1575° F, then furnace cool |
Normalizing | Heat throughout to 1650° – 1750° F, then air cool |
Carburizing & Hardening | Carburize at 1650° – 1700° F, slow cool. To harden, oil quench from 1425-1545 F |
Temper | At 250° – 350° F |
Approx Case Hardness | 60 – 62 HRC |
Approx Core Hardness | 331 – 363 BHN |
AISI 9310 STEEL Typical Core Properties after Pseudo-Carburizing:
Heat Treatment | Tensile Strength | Yield Strength | Elongation in 2″ | Reduction of Area | Core Hardness |
Pseudo Carburized 1700° F for 8 hours. Oil quenched, Tempered at 300° F for 2 hours | 187 ksi | 155 ksi | 15% | 51% | 375 Bhn |
Pseudo Carburized 1700° F for 8 hours. Slow cool to room temperature. Heat to 1425° F, oil quench. Tempered at 300° F for 2 hours | 155 ksi | 130 ksi | 15.5% | 52% | 331 Bhn |
Pseudo Carburized 1700° F for 8 hours. Slow cool to room temperature. Heat to 1525° F, oil quench. Tempered at 300° F for 2 hours | 175 ksi | 155 ksi | 16% | 53% | 363 Bhn |
Mechanical Information | |||
Density | Ultimate Tensile Strength | Yield Tensile Strength | |
Imperial | 0.284 lb/in3 | 132,000 psi | 82,800 psi |
Metric | 7.86 g/cc | 907 MPa | 571 MPa |
AISI 9310 STEEL Cold Working
Conventional methods are used to cold work AISI 9310 alloy steel that has good ductility in the tempered and hardened conditions.
AISI 9310 STEEL Welding
AISI 9310 alloy steel has good weldability characteristics as it can be welded by a standard process along with the usage of established welding methods.
AISI 9310 STEEL Forming
AISI 9310 alloy steel can be readily formed by conventional procedures as this steel has good ductility even in the tempered and quenched condition.
AISI 9310 STEEL Machinability
AISI 9310 alloy steel can be machined by conventional methods and good results are obtained when this alloy steel is machined in the tempered or annealed condition.
AISI 9310 STEEL Hardening
AISI 9310 alloy steel can be hardened by cold working or by thermal treatment and oil quenching.